Tailored precision engineering solutions
At NE Engineering, we combine cutting-edge technology with expert craftsmanship to deliver high-quality solutions that exceed expectation. With our commitment to innovation and attention to detail, we are the trusted partner for all engineering needs.
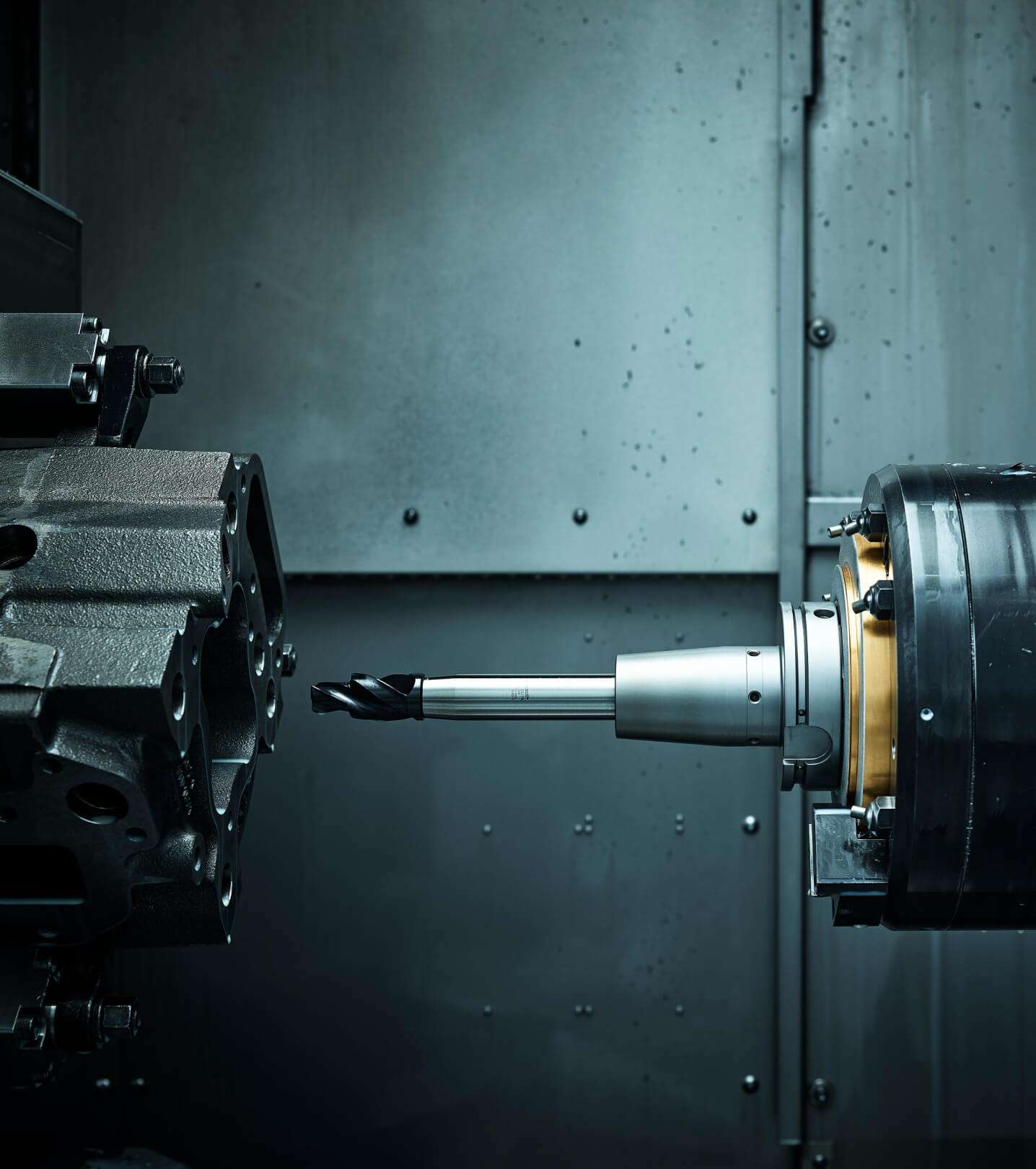
Revolutionizing the Manufacturing Process with Advanced Technology
At NE Engineering, we pride ourselves on utilising cutting-edge technology to manufacture and assemble high-quality metal pieces. Our advanced processes enable us to deliver exceptional products that meet the highest industry standards. With our focus on innovation and precision, we are revolutionising the manufacturing process.
Experience high quality metal manufacturing and assembly with NE Engineering.
Our team of experts ensure precise fabrication and time delivery, providing you with reliable solutions for your metal manufacturing needs
Delivering Quality Engineering solutions for every project
With the years of industry experience and a strong focus on customer satisfaction, NE Engineering is the trusted choice for all your engineering needs. We pride ourselves on delivering high-quality solutions that meet the unique requirements of every project.
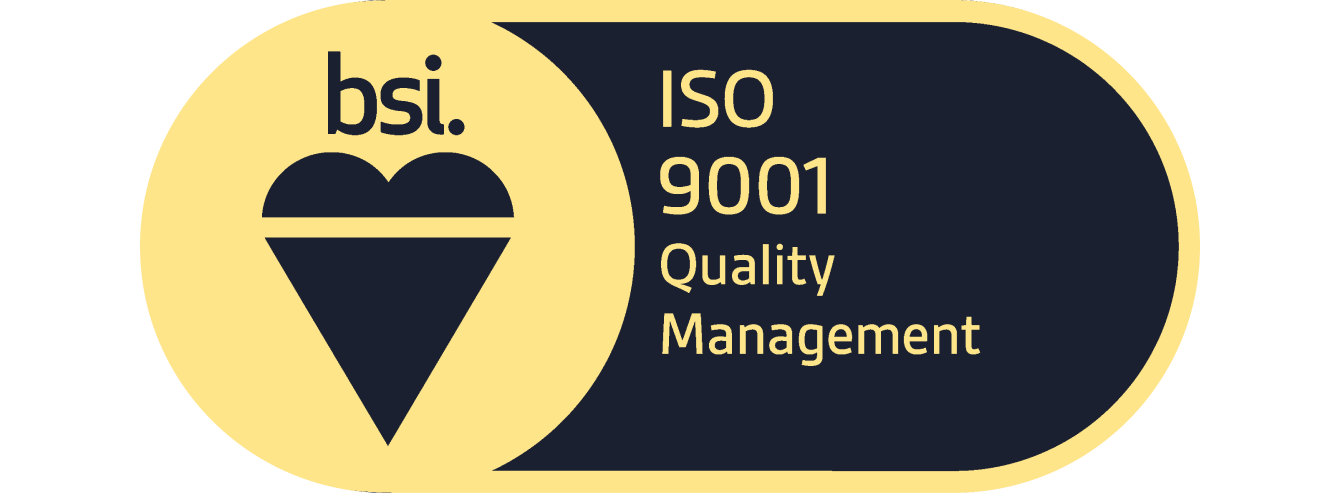